SHARE
2 Automation Solutions for the Food Industry
Not long ago, only big companies were able to automate their processes, as the required investments were really high. However, with the rise of cobots, this trend has changed and automation solutions are more affordable.
These cobots are light, flexible and easy to install and manage, since they take up little space and need no external barriers because they stop when they crash with someone or something, preventing any damage.
Today we want to show you two examples of companies that increased their productivity implementing automation solutions with a very affordable investment.
Universal Robots' cobot for Cascina Italia
What’s more, the smoothness to install and program cobots allows them to do many repetitive and different tasks like reading bar codes, making packages or placing and removing food from an oven. Cascina decided to install a UR5 cobot at one of the 24 final stations of their production line, where the cobot had to make packages of 144 cartons of 10 eggs. While before installing the cobot the plant was able to manage 2,5 million eggs per day, the robot arm was able to manage 1,5 million eggs per day, what meant a huge increase in the plant productivity. In monetary words, their initial investment of less than 17.000€ lead to a ROI of less than 1 year!
As we have seen, many companies are now installing these kind of cobot-based automation solutions, what allows them to implement affordable, efficient and flexible solutions, and many of them are asking us to do that.
After reading this article, you have the opportunity to make this technologies yourself!
Join our engineering community here
Cascina Italia
Cascina Italia is part of the family-owned company Gruppo Moretti based in Spirano, Italy, and it is dedicated to eggs and derivatives processing. They have a 22.000 m2 plant with 85 workers, where they have decided to implement a robotic arm from Universal Robots. This automation of processes is very important in the fresh food industry, where fast processes and responses to demand are crucial, and so the development of an affordable technology has allowed this kind of SME to increase their competitiveness.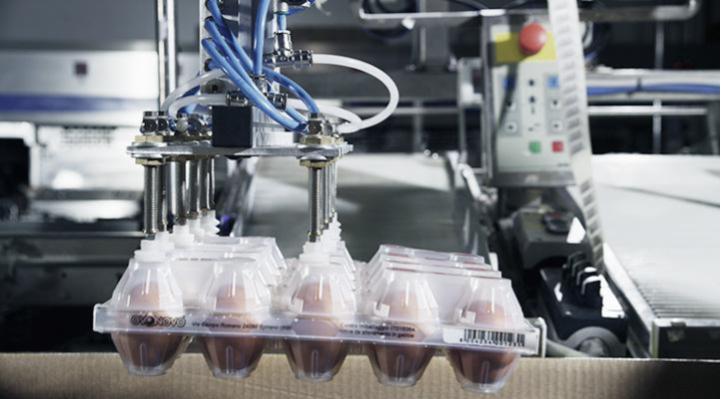
What’s more, the smoothness to install and program cobots allows them to do many repetitive and different tasks like reading bar codes, making packages or placing and removing food from an oven. Cascina decided to install a UR5 cobot at one of the 24 final stations of their production line, where the cobot had to make packages of 144 cartons of 10 eggs. While before installing the cobot the plant was able to manage 2,5 million eggs per day, the robot arm was able to manage 1,5 million eggs per day, what meant a huge increase in the plant productivity. In monetary words, their initial investment of less than 17.000€ lead to a ROI of less than 1 year!
Nortura
Nortura is a Norwegian meat products company, which is property of 31.000 farmers from all around Norway. They needed to optimize the palletizing process, but they had very limited space and budget. That is the reason why the installed a collaborative robot, which was from Universal Robots as the one from the previous example. In this case, it was the UR10, which together with a vision system, provided them the flexible solution they were looking for. This cobot allowed them to reuse space when it was not working as it only takes up 0,5 m2, between a 10% and a 20% of the space that they would need had they installed a traditional robotic arm. This technology of the cobot together with a vision system allowed them to have an accuracy of 2mm, the capacity to pile 20 pallets per day (approximately 1700 boxes per day) and the possibility to pile in two different pallets at a time. Again, it was not only a big success in terms of performance but also in terms of money as the ROI was less than a year working only one work shift, what means that it could be reduced even more as the cobot is able to work 24/7.